The Six Sigma methodology is a measurement-based strategy for process improvement and quality management. The approach is based on a straightforward philosophy — by identifying, measuring and analyzing critical metrics of your business processes, you can find ways to improve those processes and drive better results.
Want to know how you can incorporate this methodology into your organization? Read on.
In This Article
What Is the DMAIC Methodology and Why Is It Important?
The DMAIC methodology is a Six Sigma framework that involves collecting and analyzing process data to identify improvement opportunities and develop appropriate solutions.
DMAIC is an excellent methodology for complex or high-risk problems. Its rigid structure prevents users from cutting corners and skewing the data, which can damage your chances of success. It also allows for continuous improvement because companies can adjust the approach to apply lessons learned in previous studies.
That said, DMAIC is too detailed for low-risk situations with obvious solutions. Another methodology would be more fitting for these circumstances.
How to Outline the DMAIC Phases
DMAIC stands for Define, Measure, Analyze, Improve and Control. Each phase is critical to a successful process change, so be sure you thoroughly complete each step before moving forward.
D: Define
You begin the process by defining the problem you want to solve and your plan for solving it. Here’s what your summary should include:
-
- Problem statement
-
- Project scope
-
- Goal statement
-
- Business case
-
- Team responsibilities
-
- Important milestones
-
- Benefits
Remember that DMAIC studies are top-down processes, so you’ll need top management and other business leaders to sign off on your project. The summary you create in this phase can help you justify your case and win the necessary approval.
M: Measure
Next, you’ll need to determine how you will measure your progress.
Collecting good data is critical for a successful DMAIC study. The parameters you choose to quantify should be relevant to the scope and nature of your project and directly relate to the problem you are trying to solve.
You should also use suitable data collection methods to ensure you gather enough data. Some options include:
-
- Process flowcharts
-
- Run charts
-
- Gage repeatability and reproducibility (Gage R&R)
-
- Defects per million opportunities (DPMO)
-
- Process Sigma
-
- Benchmarking
One quick note on measurement methodology. Be aware of how the mere measurement effect can influence the data you collect. According to this psychological theory, when people know they are under observation, they unconsciously change their behavior — this can significantly influence your data.
You can account for the mere measurement effect by extending the measurement phase and collecting more data. The information you gather at the beginning of this phase is the most likely to be affected, so you can ignore your first few observations.
A: Analyze
Once you’ve collected all your data, it’s time to interpret it. The goal of this phase is to identify and understand the gaps between ideal and actual performance and find opportunities for improvement.
Using the right statistical tools to plot and visualize your data will help your interpretation. Some particularly helpful examples include:
-
- Histograms
-
- Time series plots
-
- Scatter plots
-
- Cause and effect diagrams
Some of these tools will make more sense for your processes than others — make sure you choose the correct method for your application to ensure accurate interpretations.
I: Improve
The insights you gained during the Analyze phase will inform the steps you take in the Improve phase. Now that you’ve identified opportunities for improving your processes, it’s time to implement those improvements.
Work with process owners and other relevant stakeholders to draft an action plan. This document should specify:
-
- The changes you plan to implement
-
- Who is responsible for making these changes
-
- When these changes will be implemented
After finalizing your action plan, you need to set it in motion. Implement all the changes outlined in your plan and test periodically to monitor their effectiveness.
C: Control
The Control phase is potentially the most critical phase of a DMAIC study because it ensures sustained performance. After all, why go to the trouble of launching the study if you don’t continue the improvements you made?
This phase often encompasses the transition from your organization’s existing processes to the new practices you defined in the Improve phase.
For example, one of the best ways to ensure success is to train all your relevant stakeholders on the improvements you implemented. Your stakeholders can understand how the processes have changed and what they should do to continue supporting the improvements.
Some useful tools for tracking success include:
-
- Flowcharts
-
- Cost savings calculations
-
- Process Sigma calculations
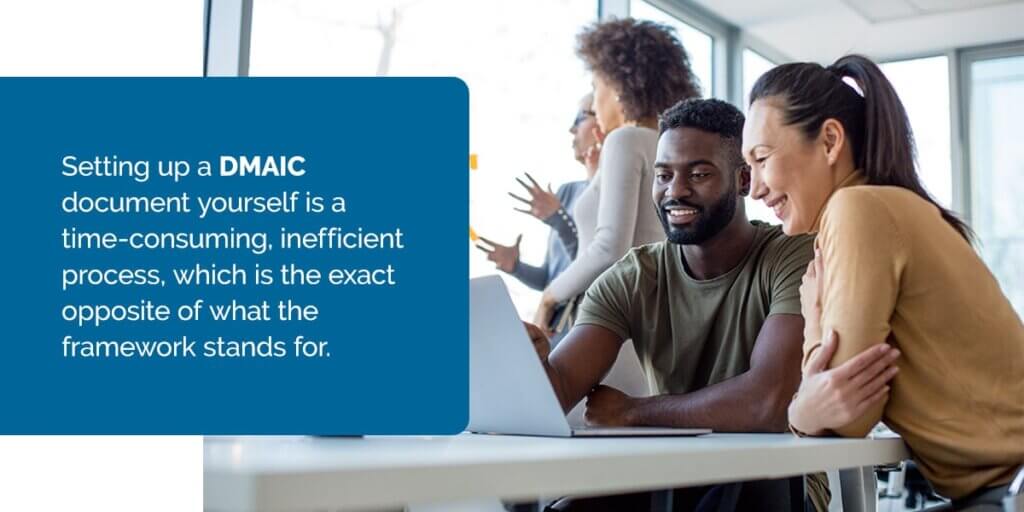
Why Use a DMAIC Template?
Organizations need a formalized document to guide them through the Six Sigma process and compile all the necessary information to properly implement this framework. Setting up a DMAIC document yourself is a time-consuming, inefficient process, which is the exact opposite of what the framework stands for.
That’s what makes a DMAIC template so useful. A DMAIC template includes headers for each phase and space to include all information and observations gathered during the process. Having this document at the ready makes getting started quick and easy — all you need to do is save a copy and you’re good to go.
Other benefits of using a DMAIC template include:
-
- Improved consistency: When you use the same format for your DMAIC studies, you make your data easier to understand for all your stakeholders and team members.
-
- Enhanced productivity: When you find ways to remove inefficiencies and streamline your processes, you’ll increase throughput and boost overall productivity.
-
- Better results: The great thing about a template is that you can optimize the process by changing the template after each study to reflect what you learned.
Common Use Cases for the DMAIC Template
One of the DMAIC methodology’s top advantages is its versatility — organizations across various industries can adopt the framework to solve inefficiencies. The Six Sigma approach can be used for the following applications:
-
- Manufacturing: The repetitive nature of most assembly line jobs present ample opportunities for data collection. By monitoring key metrics like production output and occurrence of defects, you can find ways to improve employee productivity, product consistency and overall profitability.
-
- Company culture: Human resources teams can use the DMAIC framework to improve their workplace culture. With input gained from employee complaints and suggestions, HR can identify how their current culture deviates from the company mission and brainstorm appropriate solutions.
-
- Sports: It may seem like an unlikely example, but athletes and coaches can use the DMAIC framework to identify and solve performance issues. This approach works best for individual sports because there are fewer variables to account for, but it can also be applied to some team sports.
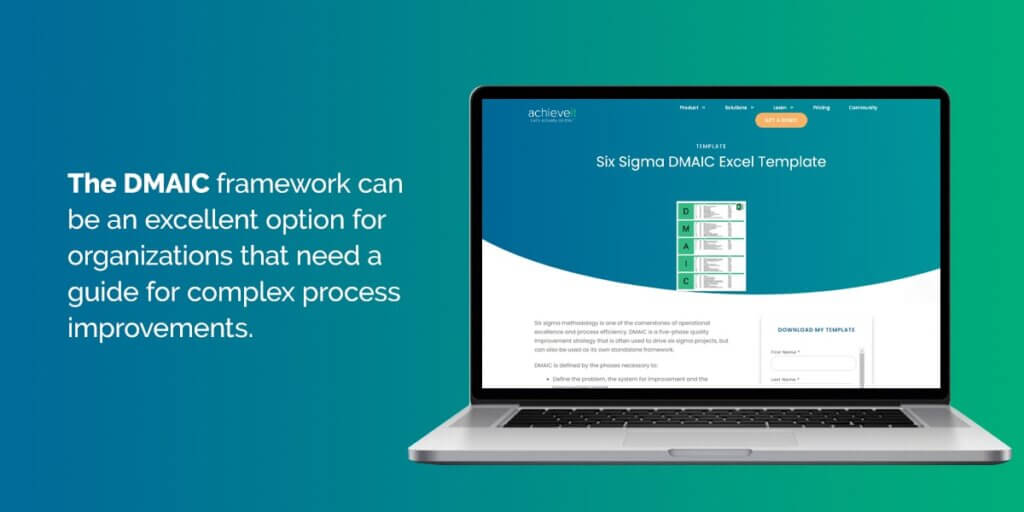
Let’s Actually Do This
The DMAIC framework can be an excellent option for organizations that need a guide for complex process improvements. Our platform is methodology-agnostic, so it’s flexible to any organization’s planning style. Download our DMAIC template to get started.
See for yourself how partnering with AchieveIt can drive better organizational results and improve your strategy execution. Contact us today to request a live demo.